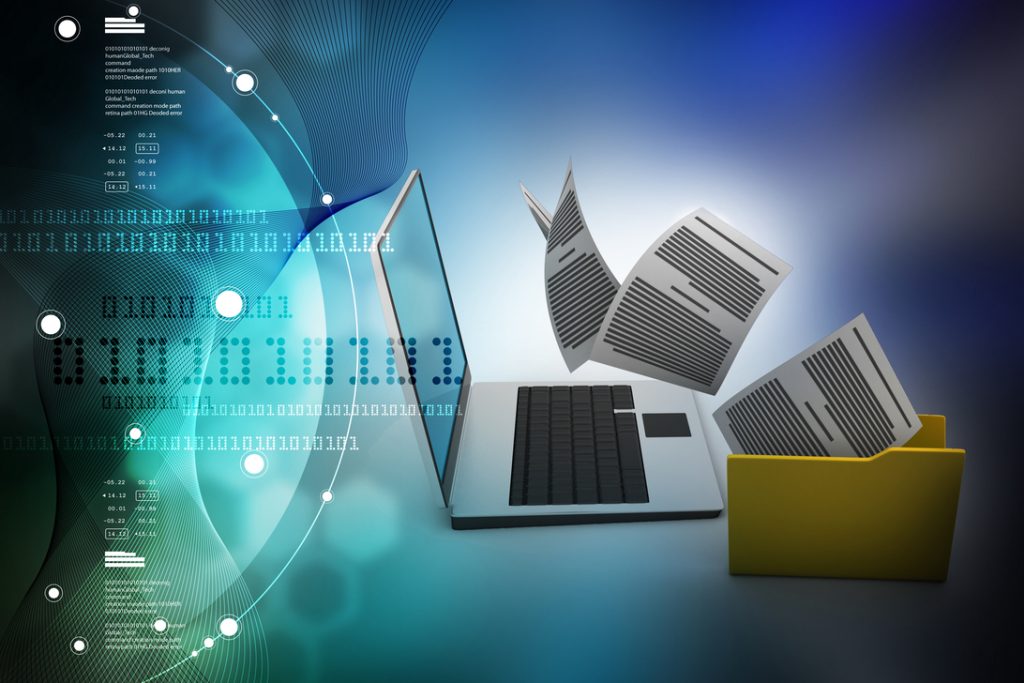
Remote operation on ships is a subject that has its roots in numerous places; the controversial concept of autonomous ships, the idea that 80% of maritime incidents are caused by human error, the trend for reducing crew numbers and as a reaction to incidents such as the grounding of the Costa Concordia.
Remote operation on ships is seen by some as a halfway step to autonomous ships but by others it is making use of technology to assist the crew of the vessel in emergencies and by providing back up under other circumstances.
The idea of autonomous ships may have been something discussed in military circles and in boardrooms of commercial equipment suppliers, but it was never really a topic that ship operators themselves had publicly debated prior to 2012 or thereabouts.
The related concept of e-Navigation was however at the heart of the EU’s ATOMOS (Advanced Technology for Optimising Manpower On Ships) project begun in 1992. The aim of this project was to reduce crew numbers on EU member state flagged vessels as a response to the lower crew costs for Asian and East European shipowners being seen as a threat to competition. One of the conclusions of the project was that modern low-manning, high-tech ships are at least as safe as conventional vessels.
In 2012, another EU funded project MUNIN (Maritime Unmanned Navigation through Intelligence in Networks) was purely concerned with developing autonomous and unmanned ships. The project completed in 2015 by which time the subject was being openly discussed and debated throughout the shipping industry.
The timing of the MUNIN project may have been coincidental but it followed rather quickly on from the grounding of the Costa Concordia in January that year. The vessel had deviated from its planned route at Isola del Giglio by direction of its captain and struck a rock formation on the seafloor. The tragedy, in which 32 people died, raised questions about the attitude of ship operators and their lack of oversight of vessels at sea and led directly to some companies including the Carnival Group to establish shore operation centres.
The matter of fully unmanned autonomous ships is still a matter or debate and while there are some projects in place, the regulatory and commercial desirability is a long way from being decided. Remote control of ships is however now a reality although not yet at a commercial operation level.
In 2017, Rolls-Royce in conjunction with tug operator Svitzer demonstrated the world’s first remotely operated commercial vessel in Copenhagen, the 28m long Svitzer Hermod. From the quayside in Copenhagen harbour the vessel’s captain, stationed at the vessel’s remote base at Svitzer headquarters, berthed the vessel alongside the quay, undocked, turned 360°, and piloted it to the Svitzer HQ, before docking again.
The tug is equipped with a Rolls-Royce Dynamic Positioning System, which was the key link to the remote controlled system. The vessel also features a range of sensors which combine different data inputs using advanced software to give the captain an enhanced understanding of the vessel and its surroundings. The data was transmitted to the remote operating centre which was designed to redefine the way in which vessels are controlled. Instead of copying existing wheelhouse design, input from experienced captains was used to place the different system components in the optimum place to give the master confidence and control. The aim was to create a future proof standard for the control of vessels remotely.
Later the same year, a team from Wärtsilä Dynamic Positioning remotely controlled a platform supply vessel in the North Sea off Scotland using a standard satellite link from its office in California 8,000km away. The satellite link included no significant latency and allowed for manoeuvring the vessel as if aboard the vessel. To make the remote control work Wärtsilä said the greatest challenge was developing a way to get sufficient data over a low-bandwidth connection but did not reveal how this was achieved. The team also needed to find a way to recover the link seamlessly if it was disrupted, and to make it secure to counter the risk of hacking.
The vessel was a 4,000dwt, 80m PSV. The control system used at the remote centre was an identical model of the ship’s integrated bridge system. Over the course of four hours the Wärtsilä team used the Gulfmark Highland Chieftain’s DP system to send it on a ‘box manoeuvre’, 20m in four directions. They then used a combination of DP and joystick control to carry out a series of other manoeuvres, testing control of surge, sway and yaw, before steering the vessel for a short distance on its journey back to Aberdeen.
In both cases, a normal crew was on board in case of problems developing, but in neither case did they have to intervene.
After the test, Wärtsilä said in a statement that the big prize in the short term is to use remote control technology to move some crew onshore, rather than to develop a completely unmanned ship. To do this, Wärtsilä is looking at using video and laser proximity sensors to allow the remote operator to have the same situational awareness as an officer on the bridge. The company did not believe this was possible with the satellite links then available but said ships could switch to 4G near the coast, so offshore crew can navigate through traffic, around obstacles, and into ports. Some degree of autonomous control will also be crucial so that the ship knows what to do if the connection is lost.
In 2020 Samsung Heavy Industries navigated a tug from a remote operations centre 150 miles away from the port. The demonstration combined collision avoidance, autopilot, and remote control technologies. The 125-foot tug operating at the Geoje Shipyard in Korea was outfitted with the company’s Samsung Autonomous Ship technology.
According to Samsung, SAS analyses in real-time signals from navigational communication equipment, including radar, GPS, and AIS, to recognize nearby ships and obstacles. The system develops the route for the vessel, evaluating the risk of collision considering the ship’s operating characteristics. It then navigates the vessel to its destination by automatically controlling the propulsion and steering.
Operators at the remote control centre were able to monitor the operations and guide the vessel with images combined with augmented reality (AR) technology. Among the tools they had was a 360-degree view around the ship that was made possible using LTE/5G mobile communication technology. At the land control centre, they viewed the images on a large screen, monitoring the operation of the ship and demonstrating the technology to directly control the tug.
Projects involving remote control as a prelude to autonomous ship operation are also underway around the globe. One of the most ambitious was to send an autonomous craft across the Atlantic. The Mayflower Autonomous Ship project has its own website (MAS400.com) from where developments can be tracked. The trimaran vessel which is around 30m began its planned voyage in June 2020 but was forced to turn back with a mechanical problem two days into the voyage. After repairs it was put back in the water in September 2020, but the planned voyage was postponed until early 2022. With no humans onboard, the research vessel uses IBM’s automation, AI and edge computing technologies to make decisions based on its status, environment and mission.
Remote assistance
The criticisms levelled against shipping after Costa Concordia galvanised some operators to establish better oversight of vessels at sea. Carnival Corporation – the parent of Costa Cruises – has been a pioneer in this respect and has established three Fleet Operation Centers (FOCs) in Hamburg (2016), Seattle (2017) and Miami (2018).
The FOC monitors all aspects of navigational safety, weather and energy management. It receives screen shot data from the bridges and engine rooms, all ships being monitored every 60 seconds and can switch to 15 second feeds if necessary. In addition, alarm status, stability information, and tank status is also transmitted. The information is displayed on a wall mounted screen display comprising several large screens allowing all relevant data and equipment status to be viewed with the need to switch screens as is necessary even on some bridge workstations which only have a single screen.
The centres are manned 24/7 always with at least two experienced mariners on hand. In the event of any safety concerns, the FOC team supports the captain and his crew on the vessel concerned. The FOC also supports the ships with regard to any non-safety-critical situations deviating from planning, such as developing gales or hurricanes which could make route alterations necessary, rescheduled sailings due to the late arrival of embarking passengers, etc.
In case a navigating ship deviates from the planned route corridor, the FOC staff receives an alert. In such cases it verifies if the deviation is comprehensible and its cause, which might be dense traffic (confirmed by reference to screen shots from radar, AIS etc). If the cause of the deviation cannot be verified, the FOC makes immediate phone contact with the ship. In a developing situation, the ship itself can make contact with the FOC seeking advice.
Collection of automated data done through the Microsoft-based ‘NEPTUNE’ platform, specifically developed for use by Carnival Maritime, allows for storing and comparing of the data of all ships monitored and supported, helping to define best-practice solutions for example for itinerary planning or engine usage on a specific route.
Carnival has built custom tools for use and integration into the FOCs such as its proprietary software applications Neptune and Argos. Developed in-house, Argos is an always-on knowledge management tool that harnesses information from thousands of data points and overlays rules-based decision making, predictive alerting and queuing into one visual dashboard. The result is at-a-glance situational awareness across the fleet which significantly improves communication from ship to shore, enhances safe passage of ships, improves operational efficiencies and supports overall environmental initiatives.
Neptune captures and provides analytics for dozens of distinct parameters for navigational safety from each ship, focusing on three strategic areas to optimise safety, efficiency and overall fleet performance.
Carnival is not the only company to operate such centres but to build three or more which can each take over if one centre goes offline for any reason is probably beyond the reach of many operators especially as Carnival’s network is built upon the company’s structure with offices for its different fleet areas.